レーザー加工はレーザーエネルギーを使用して素材の形状や外観を変質させます。このレーザーを使った素材の変質法には多くのメリットがあり、迅速なデザイン変更、機器の再設定なしでの商品製造や、製品の品質向上などが挙げられます。
また、レーザー加工は数多くの素材に対応できるというメリットもあります。対応可能な素材・材料は、セラミックス、合成物、プラスチック/ポリマー、接着剤などの非金属から、アルミニウム、鉄、ステンレス鋼、チタンなどの金属まで多岐にわたります。
レーザーエネルギー ‐ 素材の相互作用
レーザーエネルギーと素材の相互作用による効果は、レーザー波長、パワーレベル、および素材の吸収特性と化学組成に強く依存します。
レーザー加工での一般的な波長は、CO2レーザーの10.6ミクロンと9.3ミクロン、ファイバーレーザーの1.06ミクロンです。各レーザーの種類で使用可能なパワーレベル範囲があり、レーザーエネルギーと素材の相互作用を最適化することが可能です。ただし、素材の吸収特性や化学組成、および期待される加工成果によって、レーザーの種類や出力レベルの選択は大きく影響されます。
レーザーエネルギーと素材の相互作用とは、素材のアブレーションまたは素材の変質、あるいはその両方です。
- 素材のアブレーションは、素材を除去する物理的プロセスです。素材は上面から底面まで完全に除去されるか、素材の上面から特定の深さまで部分的に除去されます。素材のアブレーションは、レーザー切断、彫刻、および深さのあるマーキングに使用されます。
- 素材表面の変質は、素材の特性か外観、またはその両方を変造する物理的プロセスです。素材変質は、素材の外観や特性を変えることで素材表面上にマーキングする目的で使用されます。
切断、彫刻、およびマーキングは、一般的なレーザー加工と呼ばれています。素材の適合性によって、ひとつの素材に対して単一レーザー加工、または複数加工の組み合わせを適用することができます。
以下のチャートは、レーザーエネルギーと素材の相互作用および関連するレーザー加工の目的をまとめたものです。(図1)
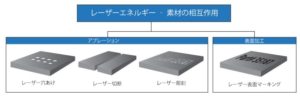
レーザー加工
レーザー切断
レーザー切断は、決められたパスに沿って素材を表面から底面まで完全除去をして分離します。レーザー切断は、単層素材でも多層素材でも可能です。
多層素材を切断する場合、レーザービームは素材の他の層は切断することなく、上層のみを切断するように正確にコントロールすることもできます。(図2)
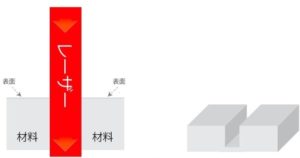
通常、波長10.6ミクロンのCO2レーザーは主に非金属素材の切断に使用されます。CO2およびファイバーレーザーはどちらも金属の切断に使用されます。しかし、原則として、金属切断には非金属素材よりも実質的に高い出力レベルを必要とします。
素材の厚さと密度は、レーザー切断時に考慮しなければならない重要な要素です。薄い素材を切断する方が、同じ素材のより厚いフォームを切断するよりも少ないレーザーエネルギーでおこなえます。通常、密度が低ければ、より少ないレーザーエネルギーですみます。しかし、一般的にレーザー出力レベルを上げると、レーザー切断の速度が上がります。
レーザー彫刻
レーザー彫刻とは、素材を表面から既定の深さまで除去することです。(図3)
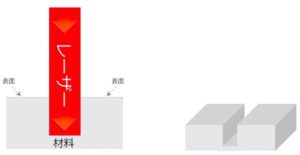
波長10.6ミクロンのCO2レーザーは、主に非金属素材の彫刻での素材除去に使用されます。素材の種類とレーザー出力レベルによって、彫刻の最大深さと速度が決まります。通常、浅彫り彫刻は、深彫り彫刻よりも速いプロセスです。さらに、低密度の素材では、高密度の素材よりも速く彫刻することが可能です。通常、レーザー出力レベルを上げると、レーザー彫刻の速度が向上します。
CO2レーザーは、レーザーエネルギーの大部分が金属で反射されてしまうため、金属彫刻には通常使用されません。しかしながら、波長1.06ミクロンのファイバーレーザーは、金属の浅堀彫刻に使用できます。
レーザーマーキング
一般的に、レーザーマーキングでは、バーコード、日付/ロットコード、製造番号または部品番号のような、人や機械が判別する識別情報を素材上に作成します。ロゴ、図、イラスト、写真などのその他の情報も素材にマーキングすることができます。(図4)
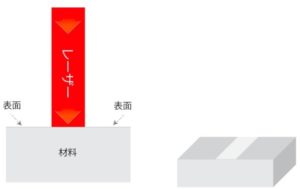
レーザーマーキングには、2つのタイプがあります。レーザーマーキングは、素材を除去して深さ(レーザー深彫りマーキング)を作る、または素材表面の色、コントラストあるいは反射率(レーザー表面マーキング)を変える加工をおこないます。
レーザーマーキングはほとんどの素材で可能ですが、その仕上がりは使用するレーザー波長によって異なります。
10.6ミクロンと9.3ミクロンのCO2レーザーは、深さのある非金属素材のマーキングと、一部の金属の表面マーキングに使用されます。波長1.06ミクロンのファイバーレーザーは、多くの材料の表面マーキング、金属の表面または浅彫りマーキングに使用されます。レーザー深彫りマーキングはレーザー彫刻とも呼ばれます。
まとめ
レーザー加工は、リアルタイムで加工可能な柔軟性を提供し、新製品の設計、開発、導入プロセスを強化します。幅広い材料に適用できるため、この技術はさまざまな業界や製造現場で利用可能な加工方法です。